two small turbos better than one big turbo
#1
Registered User
Thread Starter
Join Date: Dec 2005
Location: Europe - Finland
Posts: 74
Likes: 0
Received 0 Likes
on
0 Posts
two small turbos better than one big turbo
I have been looking into this matter whether two small chargers working in parallel are a better option that one big unit.
This is a challenging dilemma to chart out for a mere hobbyist, armed only with an internet connection to the www.
I however did manage to make a remarkable find, which now has been taken off the net (at least on the military web page where I found this info).
US armed forces launched a program to develope an all around diesel engine for a wide range of applications. This program was handed out to sub contractors who have deep technical know-how in preparing diesel engines for high power output and remarkable durability. Cummins ISB was chosen as the base engine.
Here I quote the study on achievements of this program.
--
--
Increased power output was achieved by
– High-pressure turbocharging
• The turbocharger pressure ratio was chosen to be within the
capability of current single stage production turbocharger
technology
– Single stage >3 bar
– Two modified Holset turbochargers operating in parallel
– Air to liquid charge air cooling
– Increasing the rated speed of the engine
• Several engine systems were redesigned to allow an engine
speed up to 3800 rpm
• The piston speed at 3800 rpm is 2990 ft/s (15.2 m/s), a piston
speed that is at the high limits of conventional practice
• A rated speed of 3300 rpm (2600 ft/s, 13.2 m/s) was chosen as an
appropriate trade off of engine loading and fuel consumption
The power goal was achieved with a demonstration of 500 to
550 hp from 3200 to 3600 rpm.
A 500 hp TRL 5 demonstration was completed within 6 months of
project start against a goal of 12 months.
Full power demonstration, mechanical development, and a shortened
NATO type test were performed within the goal of 24 months.
--
--
Here's a picture I found of the engine:

link to pic: http://community.webshots.com/photo/...5019242aQZops#
--
--
So far two small chargers seem the way to go.
Another find supporting this way of thinking comes from BMW.
link to page: http://www.worldcarfans.com/news.cfm...aled-uk-market
I quote:
The 335i SE Coupé accelerates from zero to 62mph in 5.5 seconds, and, if left unchecked, would travel on to an electronically-limited top speed of 155mph. This level of performance is made possible by two turbochargers, each supplying compressed air to three cylinders each. The use of two smaller units ensures that the turbochargers react more quickly to changes in the throttle position all the way to the 7,000rpm red line while also eliminating the previous scourge of turbocharged engines – ‘turbo lag’.
---
Latest breed of 6-cylinder Porsche's are a twin turbo layout as well, and have been so for a quite some number of years.
http://www.patwilliamsracing.com/2.61tt.htm
---
It would be fascinating to see someone going the extra mile, and bolting on say a pair of HX30's onto 6B and having a look what it can do.
Furthermore, how 'bout piping that setup into large bottom turbo for a two-stage charged layout.
This is a challenging dilemma to chart out for a mere hobbyist, armed only with an internet connection to the www.
I however did manage to make a remarkable find, which now has been taken off the net (at least on the military web page where I found this info).
US armed forces launched a program to develope an all around diesel engine for a wide range of applications. This program was handed out to sub contractors who have deep technical know-how in preparing diesel engines for high power output and remarkable durability. Cummins ISB was chosen as the base engine.
Here I quote the study on achievements of this program.
--
--
Increased power output was achieved by
– High-pressure turbocharging
• The turbocharger pressure ratio was chosen to be within the
capability of current single stage production turbocharger
technology
– Single stage >3 bar
– Two modified Holset turbochargers operating in parallel
– Air to liquid charge air cooling
– Increasing the rated speed of the engine
• Several engine systems were redesigned to allow an engine
speed up to 3800 rpm
• The piston speed at 3800 rpm is 2990 ft/s (15.2 m/s), a piston
speed that is at the high limits of conventional practice
• A rated speed of 3300 rpm (2600 ft/s, 13.2 m/s) was chosen as an
appropriate trade off of engine loading and fuel consumption
The power goal was achieved with a demonstration of 500 to
550 hp from 3200 to 3600 rpm.
A 500 hp TRL 5 demonstration was completed within 6 months of
project start against a goal of 12 months.
Full power demonstration, mechanical development, and a shortened
NATO type test were performed within the goal of 24 months.
--
--
Here's a picture I found of the engine:

link to pic: http://community.webshots.com/photo/...5019242aQZops#
--
--
So far two small chargers seem the way to go.
Another find supporting this way of thinking comes from BMW.
link to page: http://www.worldcarfans.com/news.cfm...aled-uk-market
I quote:
The 335i SE Coupé accelerates from zero to 62mph in 5.5 seconds, and, if left unchecked, would travel on to an electronically-limited top speed of 155mph. This level of performance is made possible by two turbochargers, each supplying compressed air to three cylinders each. The use of two smaller units ensures that the turbochargers react more quickly to changes in the throttle position all the way to the 7,000rpm red line while also eliminating the previous scourge of turbocharged engines – ‘turbo lag’.
---
Latest breed of 6-cylinder Porsche's are a twin turbo layout as well, and have been so for a quite some number of years.
http://www.patwilliamsracing.com/2.61tt.htm
---
It would be fascinating to see someone going the extra mile, and bolting on say a pair of HX30's onto 6B and having a look what it can do.
Furthermore, how 'bout piping that setup into large bottom turbo for a two-stage charged layout.
#2
Registered User
Join Date: Aug 2005
Location: fredericksburg, virginia
Posts: 3,465
Likes: 0
Received 0 Likes
on
0 Posts
Originally Posted by Artsi_L
I have been looking into this matter whether two small chargers working in parallel are a better option that one big unit.
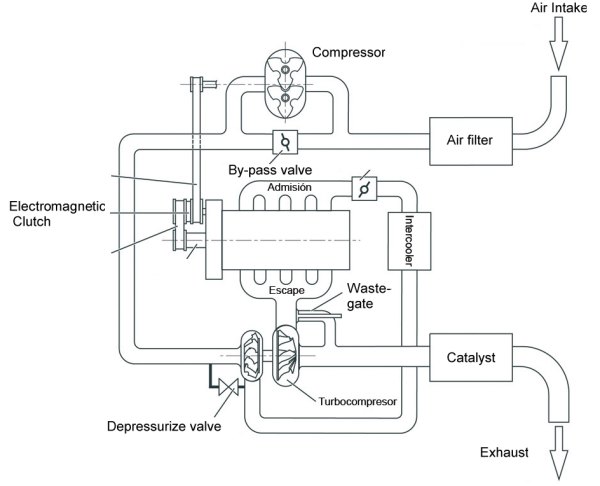
#3
Registered User
Join Date: Feb 2004
Location: south west, Michigan
Posts: 629
Likes: 0
Received 0 Likes
on
0 Posts
#5
Registered User
Join Date: Apr 2003
Location: Cummins Technical Center, IN
Posts: 6,564
Likes: 0
Received 6 Likes
on
5 Posts
Originally Posted by Ph4tty
I don't understand why you would want to do that over a compound system, especially on a I-6. I'd rather have a supercharged turbo
We can reason this through to see why this is the case. Here's a hint: linear translation or the lack of it.
First, let's draw some analogies, questions first:
1) Why does a V-12 make a lot more power than a V-6 of identical displacement and design spec?
2) Why do impact wrenches work so well compared to hammering on regular wrench?
Answer to all:
It is much more effective (in terms of power) to do a smaller amount of work more often than to do a large amount of work at a lower rate.
Your V-12 is breathing more efficiently for it's displacement than the V-6 is, so it makes more power. It will also rev faster and higher because of the lighter reciprocating mass, and will therefore have more HP.
Your impact wrench works by applying many smaller impacts at a high rate-- often 10000 blows per minute or higher! If you tried to deliver all of an impact wrench's power in a single blow, you would shatter the fastener.
Notice, it's not more EFFICIENT to "divide and conquer, but rather more EFFECTIVE. A V-12 has much higher heat loss than a V-6, which costs efficiency. But the V-12 makes more power, ceteris parabus.
So now we apply this to the parallel turbo application. The key to the success of the parallel turbo setup is that it exploits the reality that many changes in scale are NOT linear translations.
For example, if I have a wheel with a certain amount of rotational inertia, and I double the size of the wheel in all dimensions, I'd find that the rotational inertia of this larger scale version is NOT double that of the smaller-- but rather it is more likely to be FOUR TIMES that of the smaller.
The converse is also true as well. If I make the wheel HALF the size, then I might end up with only a quarter of the rotational inertia.
To in a parallel turbo configuration, you are leveraging the fact that some things translate linearly with scale and other do not.
If we went with two parallel turbos on a Cummins, we'd basically have two, 3cyl turbodiesels sharing a common crankshaft from the turbo's point of view.
So we can resize the turbo to produce HALF of the mass flow because it's feeding half of the displacement.
Yet, as we downsize the turbos, we find that the rotational inertia goes to LESS than half. To while the mass-flow requirement of our turbo system translated linearly (3 cyls need half the air of 6cyl), the rotational inertia of the turbos providing that air did NOT translate linearly.
Hence, for a given mass flow requirements, the parallel setup has a lot less lag, even though it will have higher heat loss (but probably not much higher).
JMO
Justin
#6
Registered User
Join Date: Aug 2003
Location: Jeffersonville, Ohio
Posts: 3,604
Likes: 0
Received 0 Likes
on
0 Posts
Are you thinking it will work...or not Justin??
I need to get a picture of one of our tractors...AC 4W-305, 731cu in, Parallel Chargers
Works great, too!!
Chris
I need to get a picture of one of our tractors...AC 4W-305, 731cu in, Parallel Chargers


Chris
Trending Topics
#10
The biggest problem is most people will "Y" their intake and charge hoses together making the intercooler run way hotter and beyond its cooling effeciency range.
Two air filters, two turbos, two intercoolers, custom intake w/ slightly larger plenum/smoother transition, and youre good to go.
Ill do that eventually vs the "traditional" twin turbo setup here.. Trying to make a large turbo suck 40+psi through a small one... talk about a restriction.
Two air filters, two turbos, two intercoolers, custom intake w/ slightly larger plenum/smoother transition, and youre good to go.
Ill do that eventually vs the "traditional" twin turbo setup here.. Trying to make a large turbo suck 40+psi through a small one... talk about a restriction.
#11
Registered User
Join Date: Jun 2002
Location: dfw texas
Posts: 1,771
Likes: 0
Received 0 Likes
on
0 Posts
the large turbo is not sucking anything throug the small turbo. the large turbo compresses the air, then the small turbo compresses it again. just like a 2 stage air compressor.
#12
Registered User
Join Date: Dec 2003
Location: Central PA
Posts: 839
Likes: 0
Received 0 Likes
on
0 Posts
Or, we could go a step further, and pull a trick from the MK IV Toyota Supra twin turbo.. one turbo feeds the engine at low RPM.. and you increase RPM, the second turbo gets a bit of exhaust to pre-spool it, and at a preset RPM (3500 on the Supra), a gate opens, dumping equal exhaust to both turbos. It's quite a kick in the pants when #2 fires..
Just a thought.. *stir stir*
Just a thought.. *stir stir*
#14
Registered User
Join Date: Aug 2005
Location: fredericksburg, virginia
Posts: 3,465
Likes: 0
Received 0 Likes
on
0 Posts
Originally Posted by BigBlue
I think one of the main reasons we don't do parallel on our engines is lack of space. Parallel twins require a lot of space and our engine compartment just doesn't have it.
More power to the man who makes a good working parallel system though

#15
Registered User
To my knowledge, compounds are run on diesels because of the ease with which they produce high boosts. The compression ratios of the turbos are effectively multiplied when in a compound arrangement.
Twins are run in parallel on gasoline engines because they don't use the boost pressure levels our diesels can stand. That way, they get the boost they need, while still getting the rotational inertia benefit Justin mentioned. It's a matter of what boost pressures you need.
If you look at compressor maps, you'll see that most turbos are efficient at moderate compression ratios. Trying to push most common singles to generate terribly high compression ratios is a quick way to have low efficiency and turbo parts scattered in the intercooler.
Twins are run in parallel on gasoline engines because they don't use the boost pressure levels our diesels can stand. That way, they get the boost they need, while still getting the rotational inertia benefit Justin mentioned. It's a matter of what boost pressures you need.
If you look at compressor maps, you'll see that most turbos are efficient at moderate compression ratios. Trying to push most common singles to generate terribly high compression ratios is a quick way to have low efficiency and turbo parts scattered in the intercooler.