Drag racing and thermostats
#18
Turning the heater on, can help with the pressures, but it also return hot water to the inlet of the pump. I like having cool water there.
In a closed vessel pressures are not the same, if flow through restricted passages is present. This is the case with cylinder #5. When pressures get high in the cooling system, the amount of flow around #5 gets reduced. This cylinder will overhead and score pistons and cylinders. Relieving pressure from the back of cylinder #6 (where the freeze plug normally blows), is not as good of a solution either.
Opie's system reacts to both temp and pressure. This keeps steam pockets from forming, and freeze plugs from blowing. I've only got about 50 1/4 mile passes on the truck since installing it, but so far I really like it.
Paul
My suggestion was for a cheap and easy thing to do to help mitigate the issue for the guys that run just a couple of 1/4 mile runs and have no intention of spending the money for a T and P control system for the block.
#19
DTR's 'Wrench thrower...' And he aims for the gusto...
Joined: Oct 2003
Posts: 2,668
Likes: 3
From: Smith Valley, NV (sometimes Redwood City, CA)
Camper,
There has to be very little pressure differential across the block. Not the radiator but the block itself. When the flow through the block is at it's max (full cooling) there would be the biggest differential between the pump outlet (block inlet) and thermostat. When there is no flow through the block because the stat is closed, the presssure in the block must be the same or very close to the same everywhere. I dont mean the radiator, just within the block. It can't be true to say there is more pressue at the back cylinder, but it might be hotter. The pressure that blows out the freeze plug has to be high block pressure, because of high temps, and pump head added together.
I'm speculating that the engine is building extreme pressure because it can't get rid of it's heat. This is because the t-stat is nearly closed during the run. At the start of the run the stat would be open a very small amout and it takes awhile to open fully when exposed to heat. By the time it does, the run is over and the block is very hot. The water temp at that point might be 300 degrees or higher, which might mean a block pressure of 80 psi or more. The water pump would add to this because it is pumping against a closed stat.
While the stat is nearly closed the system will experience nearly equal pressure everywhere inside the block. If the stat was completely closed the pressure would be the same everywhere in the block. From the water pump outlet to the t-stat. It has to be because it is a closed vessel at that point (the block), except for an opening from the pump. In other words the pump is pumping into a closed vessel.
So as the heat and pressure build during a run it would relieve by flowing backward through the pump. The radiator would experience system pressure and the block would experience system pressure plus water pump head pressure.
The reason the pressure goes so high is because there is no flow through the block and radiator to get rid of the heat. A tremendous inrush of energy that overwhelmes the system because the t-stat can't open fast enough to stay ahead of the rise rate.
There has to be very little pressure differential across the block. Not the radiator but the block itself. When the flow through the block is at it's max (full cooling) there would be the biggest differential between the pump outlet (block inlet) and thermostat. When there is no flow through the block because the stat is closed, the presssure in the block must be the same or very close to the same everywhere. I dont mean the radiator, just within the block. It can't be true to say there is more pressue at the back cylinder, but it might be hotter. The pressure that blows out the freeze plug has to be high block pressure, because of high temps, and pump head added together.
I'm speculating that the engine is building extreme pressure because it can't get rid of it's heat. This is because the t-stat is nearly closed during the run. At the start of the run the stat would be open a very small amout and it takes awhile to open fully when exposed to heat. By the time it does, the run is over and the block is very hot. The water temp at that point might be 300 degrees or higher, which might mean a block pressure of 80 psi or more. The water pump would add to this because it is pumping against a closed stat.
While the stat is nearly closed the system will experience nearly equal pressure everywhere inside the block. If the stat was completely closed the pressure would be the same everywhere in the block. From the water pump outlet to the t-stat. It has to be because it is a closed vessel at that point (the block), except for an opening from the pump. In other words the pump is pumping into a closed vessel.
So as the heat and pressure build during a run it would relieve by flowing backward through the pump. The radiator would experience system pressure and the block would experience system pressure plus water pump head pressure.
The reason the pressure goes so high is because there is no flow through the block and radiator to get rid of the heat. A tremendous inrush of energy that overwhelmes the system because the t-stat can't open fast enough to stay ahead of the rise rate.
#20
Raspy - you clarified your first post as saying the closed system is just the block. I did not see that as your meaning as the entire cooling system is typically referred to as a closed loop system and there have been people on this board who say the block runs at 15 PSI as that is what the pressure says on the radiator cap!! As you know that is not the case.
Below is a flow diagram of the cooling system of the 5.9 and you will note that the back of the engine get its water after it has already passed over the first five cylinders. Flow from each cylinder then goes up to the head and then forward to the thermostat (the head is not shown but that is what happens)
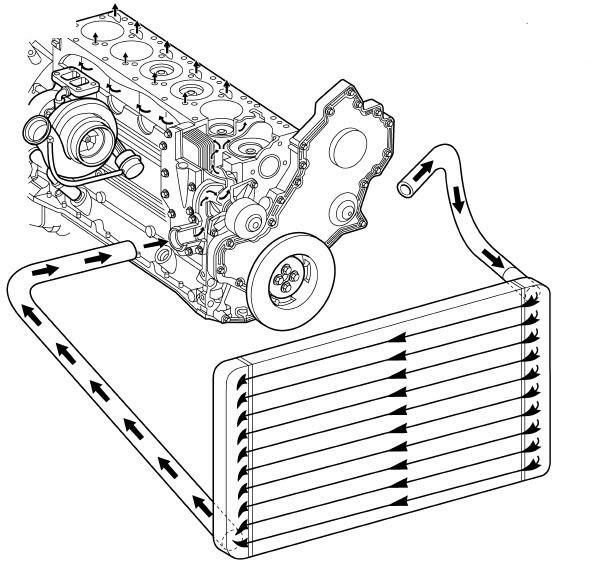
One of the theories on why the rear blow out is due to dead heading. During rapid accel the pump hits the block with several waves of pressure as the rpm go up and down rapidly (shifting) . These can impact the rear of the engine more as there is no easy way for the pressure waves to be dissipated. That is where the heater core flow comes into play. It takes its flow from the top of the head between 5 and 6 and is in a good spot to minimize the pressure spikes and puts it back to the inlet to the pump (again not shown but please trust me on that).
I am not sure the water takes up as much temperature as fast as you suspect but it could and the block water flow sure does not help prevent it. So opening the cab heater core sure could not hurt.
Below is a flow diagram of the cooling system of the 5.9 and you will note that the back of the engine get its water after it has already passed over the first five cylinders. Flow from each cylinder then goes up to the head and then forward to the thermostat (the head is not shown but that is what happens)
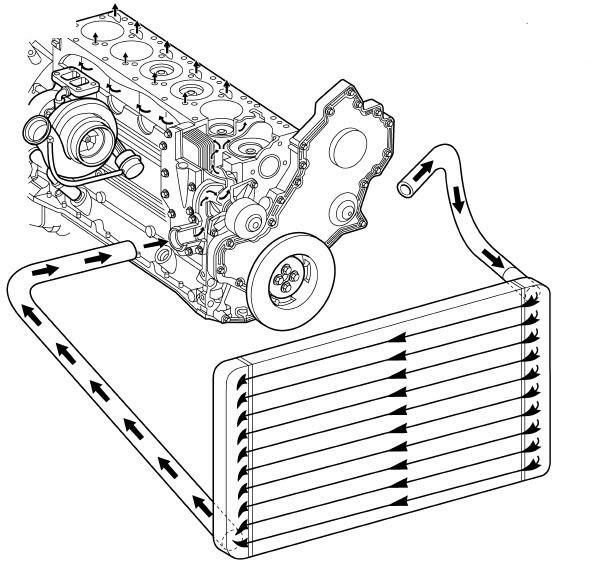
One of the theories on why the rear blow out is due to dead heading. During rapid accel the pump hits the block with several waves of pressure as the rpm go up and down rapidly (shifting) . These can impact the rear of the engine more as there is no easy way for the pressure waves to be dissipated. That is where the heater core flow comes into play. It takes its flow from the top of the head between 5 and 6 and is in a good spot to minimize the pressure spikes and puts it back to the inlet to the pump (again not shown but please trust me on that).
I am not sure the water takes up as much temperature as fast as you suspect but it could and the block water flow sure does not help prevent it. So opening the cab heater core sure could not hurt.
#21
DTR's 'Wrench thrower...' And he aims for the gusto...
Joined: Oct 2003
Posts: 2,668
Likes: 3
From: Smith Valley, NV (sometimes Redwood City, CA)
Camper,
I'm sure the heater core flow will help some, but the real fix is to bypass the t-stat.
I'd like to see a pressure recording device attached during a run to see what the pressures are getting up to. Also the temps. I just can't believe the pump is putting enough pressure into the system to blow out the plug, pressure wave or not.
It would be fun to put some instruments on and check it out. Even just a direct reading pressure gauge that the driver could watch.
If your theory is correct and it's all about pressure from the pump it could be tested in the driveway while cold just by reving it up.
It's late here and I've had a beer or two, but it would be fairly simple to calculate how many BTUs are delivered to the engine block and it's final temp after a run. The approximate efficiency of the engine, horsepower, time, starting temp of the system and rough specific gravity of the iron and water exposed to the heat. Assuming a closed stat for demonstration purposes, the total rise in temp might be 80 degrees or something. With a starting temp of 190 degrees it would add up to 270 degrees. That might be about 50 psi. Then add the pump head of X and you are close to the block pressure.
The reason this is so much more than 15 psi is that the radiator is out of the flow loop and cannot get the temperature down because the stat is closed. As I mentioned earlier, the radiator should see block pressure minus pump head. And the rise rate was so high that the small 3/8 overflow tube at the radiator cap gets overwhelmed. Of course it's all a spike that happens in about 20 seconds or so and then it's over.
Does that make sense? It would be fun to test it out.
I'm sure the heater core flow will help some, but the real fix is to bypass the t-stat.
I'd like to see a pressure recording device attached during a run to see what the pressures are getting up to. Also the temps. I just can't believe the pump is putting enough pressure into the system to blow out the plug, pressure wave or not.
It would be fun to put some instruments on and check it out. Even just a direct reading pressure gauge that the driver could watch.
If your theory is correct and it's all about pressure from the pump it could be tested in the driveway while cold just by reving it up.
It's late here and I've had a beer or two, but it would be fairly simple to calculate how many BTUs are delivered to the engine block and it's final temp after a run. The approximate efficiency of the engine, horsepower, time, starting temp of the system and rough specific gravity of the iron and water exposed to the heat. Assuming a closed stat for demonstration purposes, the total rise in temp might be 80 degrees or something. With a starting temp of 190 degrees it would add up to 270 degrees. That might be about 50 psi. Then add the pump head of X and you are close to the block pressure.
The reason this is so much more than 15 psi is that the radiator is out of the flow loop and cannot get the temperature down because the stat is closed. As I mentioned earlier, the radiator should see block pressure minus pump head. And the rise rate was so high that the small 3/8 overflow tube at the radiator cap gets overwhelmed. Of course it's all a spike that happens in about 20 seconds or so and then it's over.
Does that make sense? It would be fun to test it out.
#22
An old trick I used to use running circle track was to take an old t-stat and gut it out so that all that was left was the outer ring and then re-install it. I found that doing that provided just enough restriction to slow the coolant down enough to provide a constant temp. without creating the pressure spikes you get with a normally operating t-stat. I don't know just how effective that would be in a diesel on the drag strip but......
#23
#25
Intelligent Engineering
Paul
#26
Another quick note. The heater core in our trucks is always "on". The blend doors in the heater just changes where the air comes from (eg. through the heater core or from the outside). If you do turn the heater on, with the fan blowing then it can act like a mini rad, but it's pretty small. The water flow is unchanged though.
Paul
Paul
#27
Granted we have much warmer ambient temps than many but I have never had a problem "taxi-ing" around the parking area and return lanes, at the track, to get everything up to temp. I use 1st gear and 2000 rpm. A 180* T-stat helps a lot. Stock 3rd Gen still 190*??
Quite honestly, I worry more about cold oil than cold coolant..... but I'm not a third gen.
If more drag racing CTD's had oil temp gauges they might share my concerns; with good quality oil... you gain HP with warmer oil.
I once watched Warren Johnson test HP against Oil Temps. He gained 3 HP for every 10* above 180*..... all the way up to 230*
Granted this is a 1600 hp ProStock gasser and not a diesel, but I think the principle may still apply.
RJ
Quite honestly, I worry more about cold oil than cold coolant..... but I'm not a third gen.

If more drag racing CTD's had oil temp gauges they might share my concerns; with good quality oil... you gain HP with warmer oil.
I once watched Warren Johnson test HP against Oil Temps. He gained 3 HP for every 10* above 180*..... all the way up to 230*
Granted this is a 1600 hp ProStock gasser and not a diesel, but I think the principle may still apply.
RJ
#28
Another quick note. The heater core in our trucks is always "on". The blend doors in the heater just changes where the air comes from (eg. through the heater core or from the outside). If you do turn the heater on, with the fan blowing then it can act like a mini rad, but it's pretty small. The water flow is unchanged though.
Paul
Paul
Thread
Thread Starter
Forum
Replies
Last Post
expressfish
3rd Gen Engine and Drivetrain -> 2007 and up
3
03-08-2007 11:18 AM